必要とする人のために、高機能なカスタムメイドの義手を作り、手の届く価格で提供したい――その情熱が、22歳の米国の起業家Easton LaChappelleを突き動かし、最先端の3Dプリント技術を駆使したロボットアームの製造企業「Unlimited Tomorrow」を創立するに至った。従来の義肢業界に風穴を開けるべく現れた革命児、LaChappelle氏の軌跡とUnlimited Tomorrowの活躍に迫る。
原点は、14歳で作ったロボットアーム
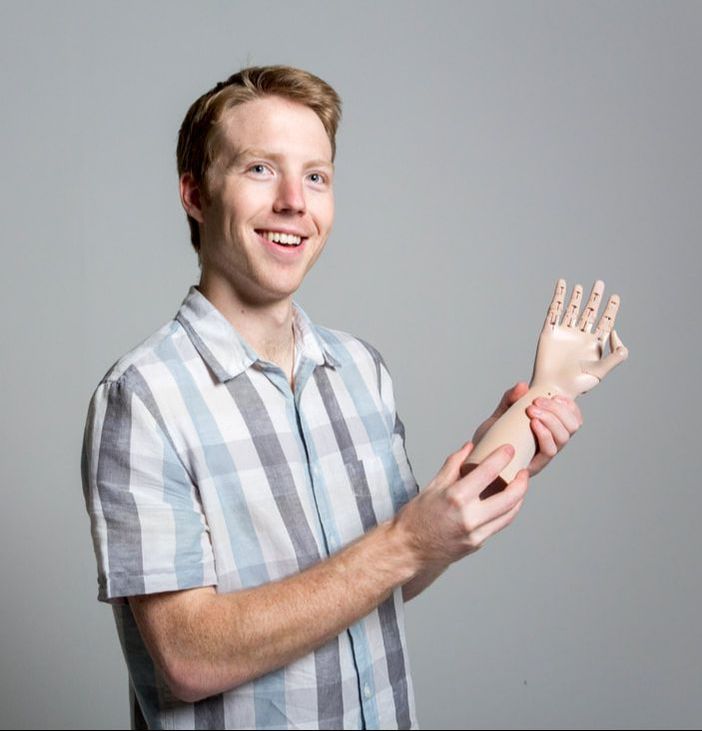
引用元:Unlimited Tomorrow https://www.unlimitedtomorrow.com/
LaChappelle氏が初めてロボットアームを作ったのは、14歳の時。レゴブロックと釣り糸、電線管、模型飛行機の小さなモーターを組み合わせたもので、当初は、「面白半分でやってみた」と回想するが、それ以来、より精度を上げるための方法を探すために、インターネットで情報収集し、独自に改良を重ねていく。彼の生まれ故郷、コロラド州の田舎町で得ることができない情報については、ロボットとエンジニアリング分野の専門家たちに、直々にメールを送り、スカイプでインタビューを行うなど、体当たりのアプローチで、水を得た魚のごとく、義手開発のノウハウを培っていった。
2011年、16歳の誕生日に、500ドルの3D プリンターを両親と折半して購入し、ワイパーモーターで駆動する3Dプリント義手を製作した。EEGヘッドセットを通して伝わるユーザーの脳波信号によって動かすことができる、というもので、LaChappelle氏は、この義手を科学展覧会に出展し、グローバルサイエンス賞(高校生の部)を受賞。当時の米国の大統領、バラク・オバマ氏と接見したほか、NASAの夏季インターンシップを経験する機会などに恵まれた。
たったひとりの少女のために
6年をかけて、3Dプリント義手を開発
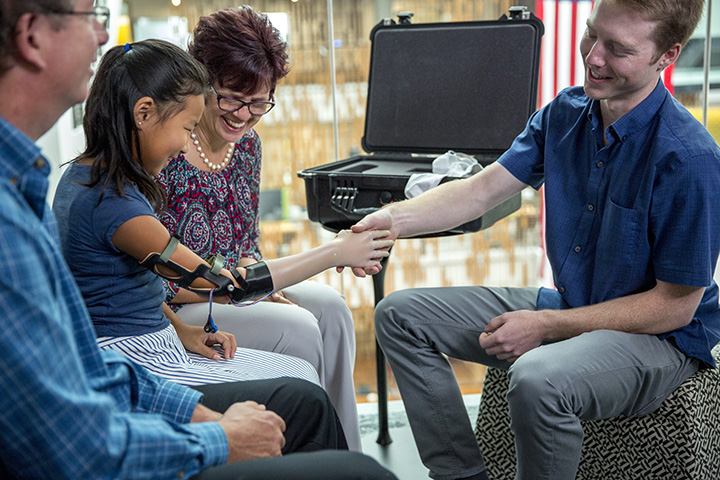
引用元:Microsoft
https://news.microsoft.com/features/high-fives-around-young-inventor-fits-girl-robotic-hand/
この科学展覧会では、LaChappelle氏にとって、その後の人生を大きく左右する運命的な出会いがあった。彼女の名は、Momo。生まれつき右腕の肘から先のない幼い少女は、群衆をかき分けて飛び出し、彼の作った義手の指が動くのをじっと見つめていた。その時、Momoがつけていた義手は、手のひらを開いて、閉じるという動作しかできないもので、“かぎ爪”のような形状をしていたという。
「(Momoの両親によると)その義手は、80,000ドルもするのです。私は、たった数百ドルで、より優れた機能を備えた義手を作れたというのに」
その時、目からウロコが落ちる想いがしたという。特に、子どもの場合、洋服や靴と同じように、成長と共に、義手もサイズが合わなくなり、新たに買い換える必要が出てくる。高価な義手を子どもに与えることには、さまざまな問題があり、また、それらの義手は、多くの人にとって、あまりにも高すぎるため、手の届かないものでもある。
Momoとの出会いをきっかけに、LaChappelle氏は、学校には行かず、彼女の義手を作り上げるための研究やテスト作業に専念した。マイクロソフトをはじめ、Unlimited Tomorrowの設立に協力したトニー・ロビンズ氏など、さまざまなサポートを受けながら、実に6年もの歳月を費やし、思い描いた通りの3Dプリント義手を完成させた。
2018年末までに、カスタムメイドの
3Dプリント義手100本を生産予定
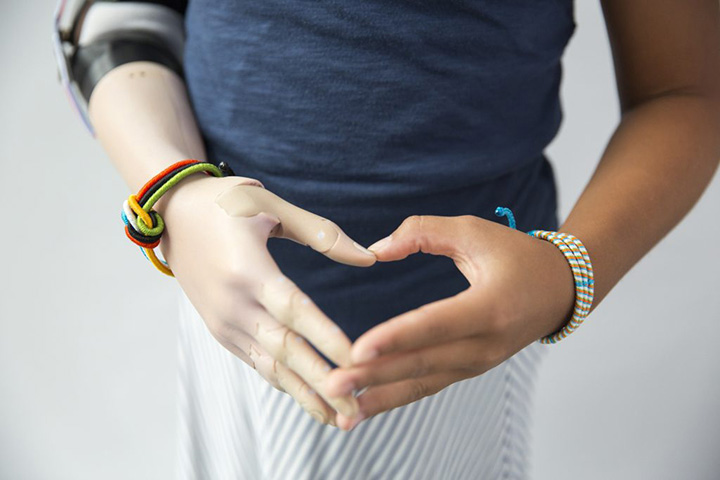
引用元:Microsoft
https://news.microsoft.com/features/high-fives-around-young-inventor-fits-girl-robotic-hand/
Momoのために開発した義手は、筋肉制御が可能で、指の1本ずつに触覚のフィードバック機能があり、物を触った感覚を得られる。義手の表面の色は、好みの色にカスタマイズできるし、爪には、色を塗ることだってできる。
こうして、ロボットアーム第1号を世に生み出したLaChappelle氏。現在、Unlimited Tomorrowは、前述のマイクロソフトのみならず、3Dプリント技術の専業メーカーのストラタシスや、3Dソフトウェアプロバイダーのダッソー・システムズといった大企業と提携し、2018年末ごろまでに、個人向けの義手100本を生産する予定で、製作に取り掛かっている。これら2社とのコラボレーションにより、開発のスピードをさらに加速させると共に、一人ひとりに合ったカスタムメイドの義手を作るために、重量やコスト面などを考慮しながら、改良を重ねているところだ。
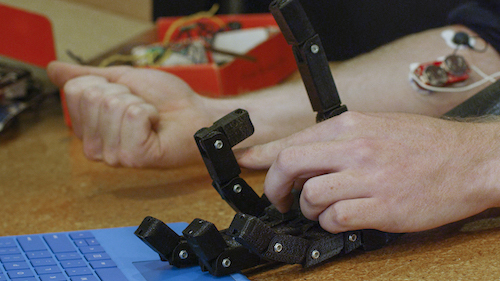
引用元:Rapid Ready by Digital Engineering
http://www.rapidreadytech.com/2018/02/unlimited-tomorrow-redesigns-the-prosthetic-arm/
Unlimited Tomorrowの公式サイトによると、現段階において、カスタムメイドの義手の製作期間は、約1~2週間、重量は1ポンド(0.45kg)。1本20,000 ~ 100,000ドルと、極めて高価な義手が大半を占める義肢業界において、その4分の1に相当する価格、あるいは、それ以下で手に入れられるとしたら――「義手の指を自分で動かす」という一番の夢を叶えたMomoのように、世界のどれほど多くの人が喜びを得て、人生を豊かにすることができるだろうか。若き起業家、Easton LaChappelleの革命は、ここからが本番だ。
UNLIMITED TOMORROW
https://www.unlimitedtomorrow.com/
[TOP動画引用元:https://youtu.be/HNvLtst7Gjo]